as recalled by LaMont Matthews and John Sewell, March 2013
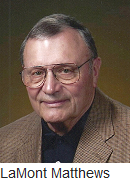
CH2M HILL in the 1960s and 1970s was a particularly exciting place to be. There were major public support and grants available for water and wastewater work, and we were the “go to” firm wherever we had a presence. The water and wastewater groups were developing cutting edge treatment systems; and the mechanical, electrical, and I&C groups were thriving in the creative atmosphere we enjoyed.
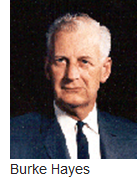
The first of these was the Model A Flomatcher invented and patented by Burke Hayes. This unit consisted of a stack of rheostat plates immersed in the raw sewage in the headworks pump station at a wastewater treatment plant. As the sewage level rose and fell, the speed of the lift pumps increased and decreased to maintain the level of the wet well within a narrow band.
This unit replaced the float-operated level control systems then in place, resulting in some major advantages. One was a huge reduction in wet well size. Each pump float control needed a wide band of level change to start and stop the pumps in sequence, and the wet well needed to be sized accordingly. With the Flomatcher, spacing and submergence of the pumps became the criteria. The size of the wet well was reduced by factors of 2 or 3. The other advantage was a much smoother flow to the treatment plant. The cost savings and operating advantages gave us a leg up on the competition, and we virtually owned the business wherever we were located.
The next step was the development of the Model B unit by Carl Ryden, the Chief Mechanical Engineer in Corvallis. This unit used a bubble tube to measure the wet well level so the plates no longer had to be directly in the sewage, thereby eliminating some nasty corrosion problems. It also allowed the control unit to be located remotely in areas much more convenient for the operator. This is the unit that provided the basis for separately marketing the Flomatcher.
Closely following the Model B was a whole flurry of system design improvements to contribute to our growing success. In no particular chronological order, they were:
- Adaptation of industrial pneumatic proportional control systems to municipal applications
- Induction engine generators operating on digester gas
- Heating digesters using a hot water jacket heat exchanger around the mixer
- Detailed surge analysis resulting in major changes in pressure control systems
- Air pollution control work in industrial applications
These will be expanded below.
Authors’ Caveat: This list and the subsequent discussion are based entirely on our memory and has not been cluttered with any research. If the reader remembers it differently, then you may be right, too.
Pneumatic Control Systems
In the early 1960s, pneumatic control systems were the standard in industrial boiler plants, while municipal systems still relied on float switches and direct float-operated valves as the accepted technology. To the best of my knowledge, the first major application of this system was at the Corvallis Water Treatment plant expansion in about 1962. The system was designed by LaMont Matthews with some valuable consulting from Austin Evanson and featured a very primitive version of what was later termed P&IDs. These controllers were proportional; that is, they were smooth, gradual changes rather than the abrupt changes inherent in float-based systems. Because this was also our first large-scale application of the Microfloc filter bed technology, proportional control was doubly important. From this point on, this technology was used in all our control applications.
Induction Generators
Using induction generators driven by sewage gas-fueled engines enabled us to install these systems in small- to medium-sized plants simply and economically. An induction generator is just an electrical motor that is operated at higher than synchronous speeds with field excitation from the power company. This causes the unit to be automatically synchronized with the plant power system and eliminates the need for expensive, complicated synchronizing controls that would be beyond the scope of most small plant operators. The waste heat was recovered from the engine for digester heating, making the overall efficiency of the system very high. Again, this was a collaboration between Austin and LaMont, with the first application at the new Willow Lake Wastewater Treatment Plant in Salem, Oregon.
Digester Heating
Wrapping a jacket around the digester mixer draft tube and using circulated hot water as the heating medium was another one of Carl Ryden’s contributions. Prior to that, the digester was heated using an external heat exchanger. This was a spiral-shaped monstrosity that required a complete sludge pumping and piping system to circulate the sludge from the digester to the heat exchanger and back again. It was easy to take apart for cleaning, which was a good thing because it happened often. Contrast this with two 3/4-inch pipes circulating hot water through the internal exchanger. This was another home-grown industry standard.
Surge Analysis
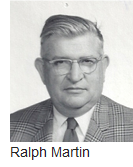
Ralph Martin brought the sophisticated methods for analyzing pressure surges in pipelines from his work on the Eugene Water and Electric Board’s hydroelectric projects. This allowed us to use slow-operating control valves and vacuum breakers to limit pressure surges on long water pipelines and sewage force mains. Before this, the accepted process was the use of very large hydro pneumatic tanks and air compressors to cushion the pressure rise.
Air Pollution Control
When Rick Reid joined the firm in the late 1960s, he brought an interest and skills in the field of air pollution control, which was just then drawing the attention of regulatory authorities. The early demand for this service was in the boiler plants of the wood products industry. This is important to mention here because it was our first entree into the process side of the industry, which was picked up by Ken Durant in the Portland office and aggressively marketed to industry. This resulted in our establishing a position in the overall environmental permitting for new industrial construction. And, it became the base for the eventual formation of the Industrial Design Corporation (IDC) that, as a subsidiary, became the major design firm for the electronics industry.
Instrumentation & Control Systems
The 1970s was a time of major change for CH2M HILL: Projects became significantly larger and more complex than ever before. New design tools and project management practices were required to facilitate coordination and integration of these increasingly complex systems, particularly in the areas of process, mechanical, electrical, and instrumentation and controls.
Also in the 1970s, major changes evolved in the area of Instrumentation & Control (I&C) systems. Early in that decade, we saw the decline of pneumatic controls (3-15 psi) and the overwhelming rise of electronic controls (4-20 maDC). The most dramatic and far-reaching change came with the advent of digital systems. First were programmable controllers, which replaced relay logic. Then computer-based control systems evolved with CH2M HILL leading the way as the first company to successfully apply a computer-based control system to a civil engineering project, UOSA. Digital technology has now, of course, exploded to encompass every aspect of process instrumentation and control.
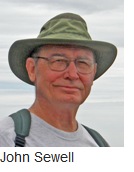
These times of change were vast and exciting and required a corresponding evolution in the ways CH2M HILL practiced I&C system design and delivery.
Led by John Sewell, the embryo of what became the I&C Discipline began in the early 1970s as a group of six engineers in the CVO, RDD, and SEA offices. We called ourselves I&C Coordinators. The group shared I&C experiences and concepts and collaborated to create methods and practices to meet the unique needs to deliver I&C systems.
The group recognized that their work, by its inherent multidiscipline nature, uniquely resided at the center of the overlaps between process, mechanical, and electrical engineering aspects of project delivery. We saw our position as providing a unique opportunity to help the project teams achieve the much needed multidiscipline coordination/integration. The tool was, of course, the Process & Instrumentation Diagrams (P&IDs).
P&IDs quickly became a standard component of any significant multidiscipline project and, indeed, provided both assistance to the integration of the various design efforts of the other disciplines and the development and delivery of I&C systems. CH2M HILL was the first civil engineering firm in the country to employ P&IDs.
As the firm grew, more and more complex multidiscipline projects were undertaken. With the growing need, the I&C group also grew. From that informal association of six people, the I&C gang grew to be an official discipline with over 120 members in the 1990s. It is notable that CH2M HILL was the first civil firm to recognize and establish a separate I&C discipline. Many other civil engineering firms now emulate the CH2M HILL I&C practices and procedures, both drawings and specifications. Many now have I&C groups.
Summary
The firm reorganized into the discipline system in the early 1970s with Burke Hayes as the Director of the Industrial and Energy Systems discipline. He gathered the firmwide mechanical and electrical operations into this discipline, which eventually included Mechanical, Process Electrical, Electric Utilities, Instrumentation and Control, Corrosion, Industrial Design, and even Mining Engineering. LaMont succeeded Burke upon his retirement in 1976. When LaMont retired in 1996, the discipline had grown to 220 people firmwide with an assigned gross income of over $20 million.